2025
Real-Time Triangle-SDF Continuous Collision Detection
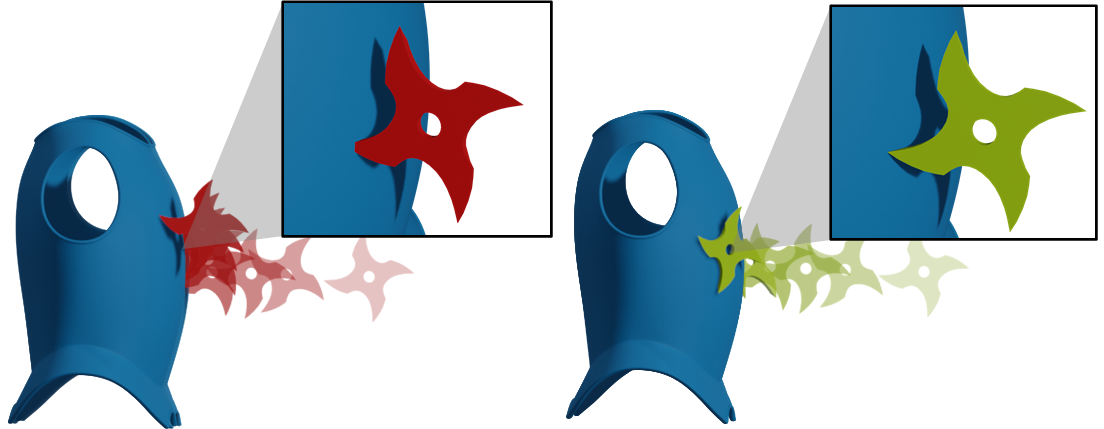
Real-Time Tri-SDF CCD? See how the we made this all possible in this paper.
2024
Adaptive Methods for Elastic Deformation
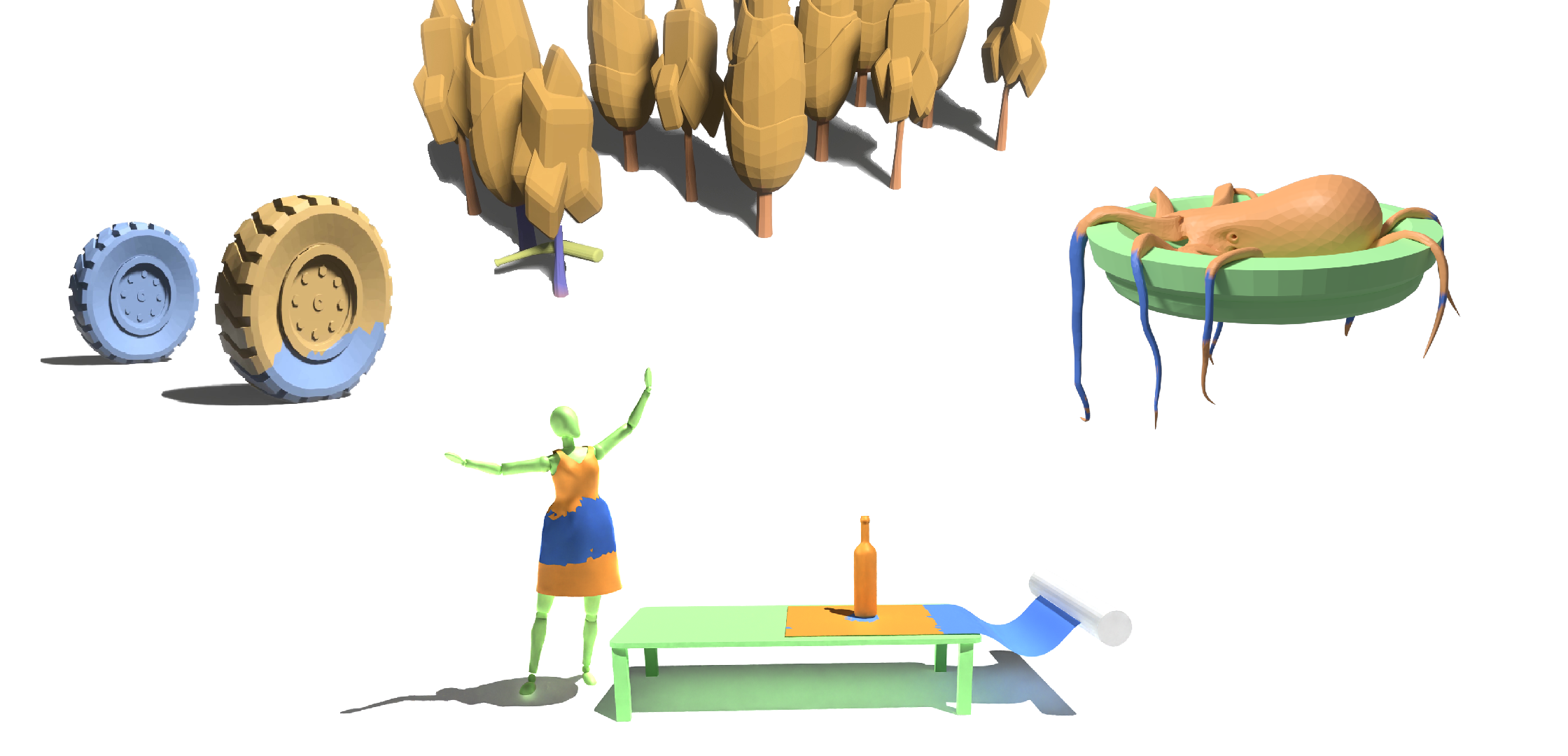
Really just a big passion project of mine.
A Multi-Layer Solver for XPBD
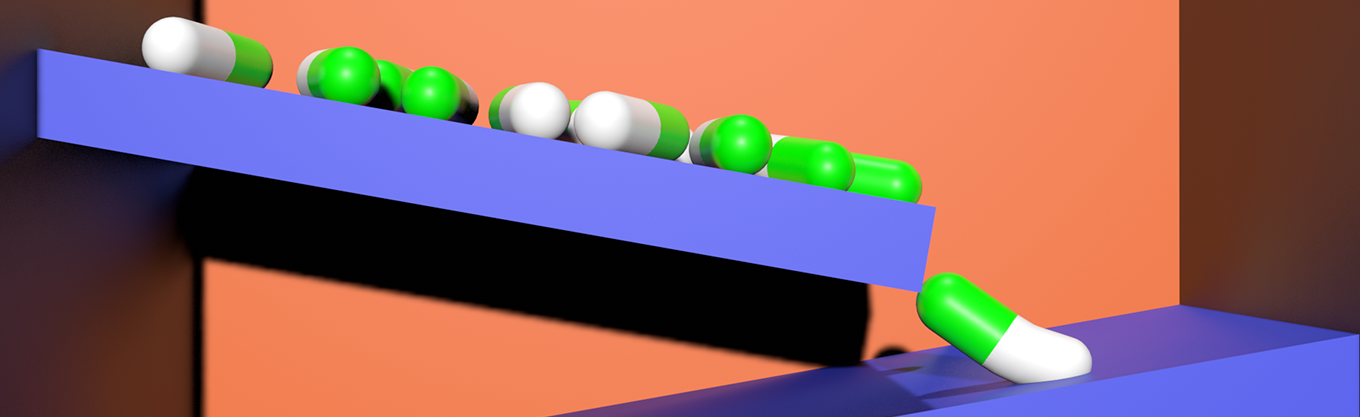
Want rigidification without the drawbacks of adaptivity? Use this multigrid-like solver.
2023
Adaptive Rigidification of Discrete Shells
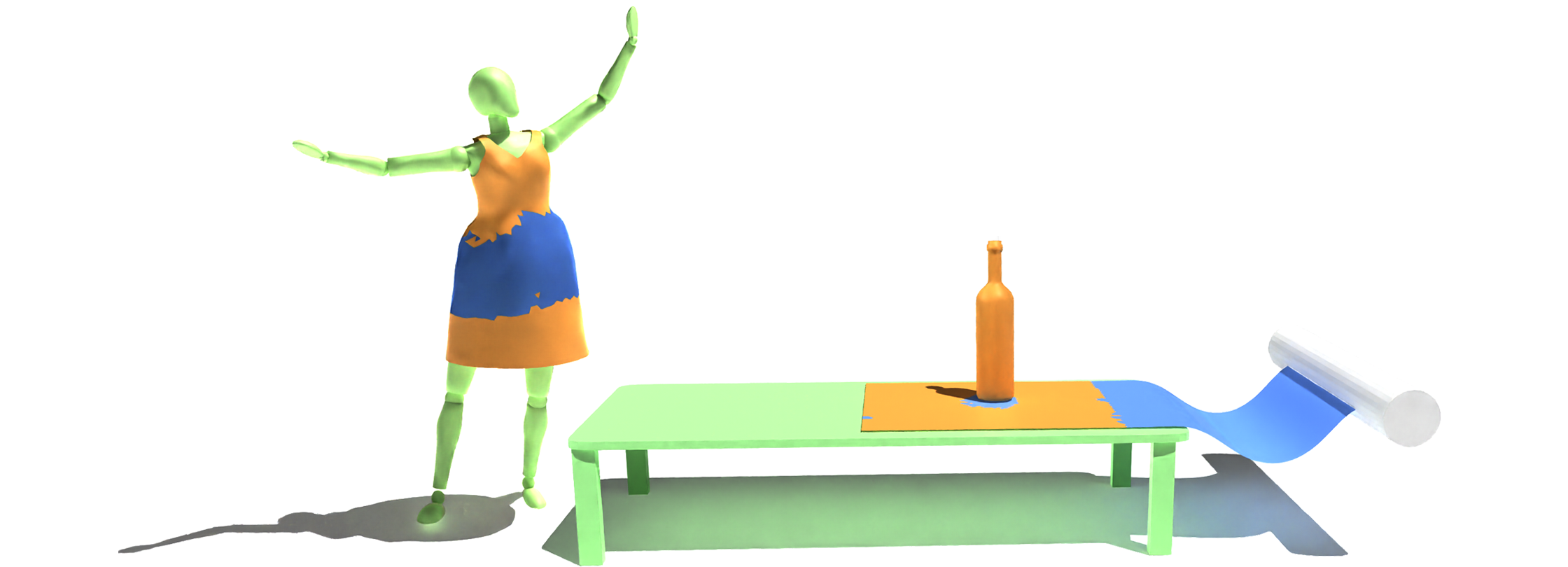
Methods like remeshing target mostly flat regions of shells. We excel at coarsening curves.
2022
Adaptive Rigidification of Elastic Solids
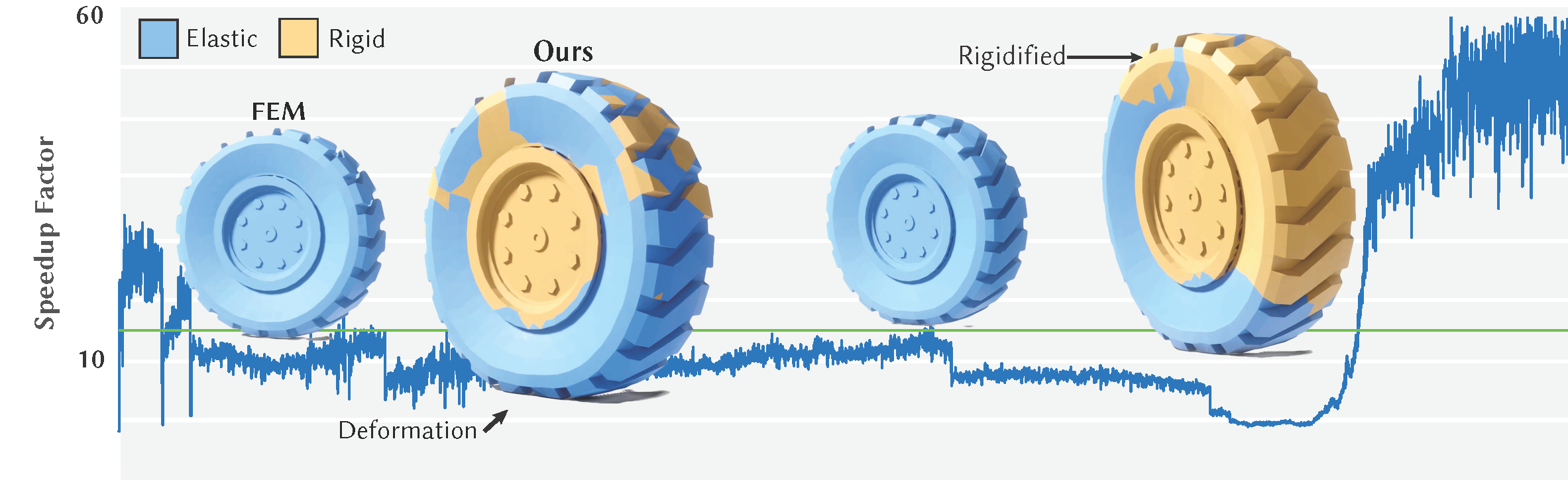
Why waste resources computing deformation on non-deforming regions? Use our method instead.
2020
Ordonnancement de tâches sous contraintes sur des métiers à tisser
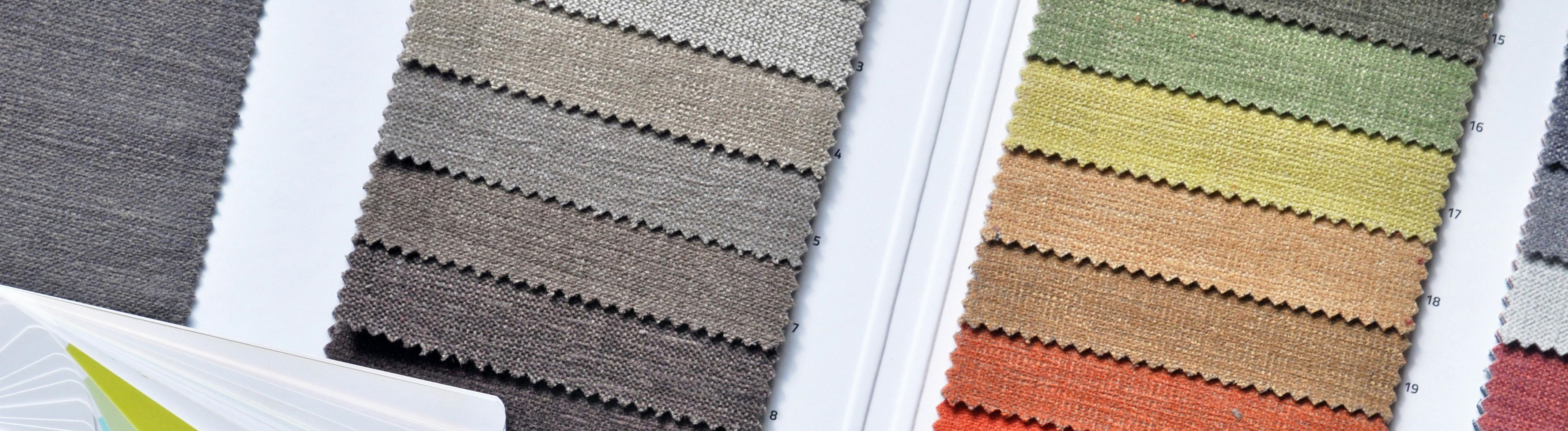
Generate schedules for looms using fancy methods.
The CONFIDENCE Constraint: A Step Towards Stochastic CP Solvers
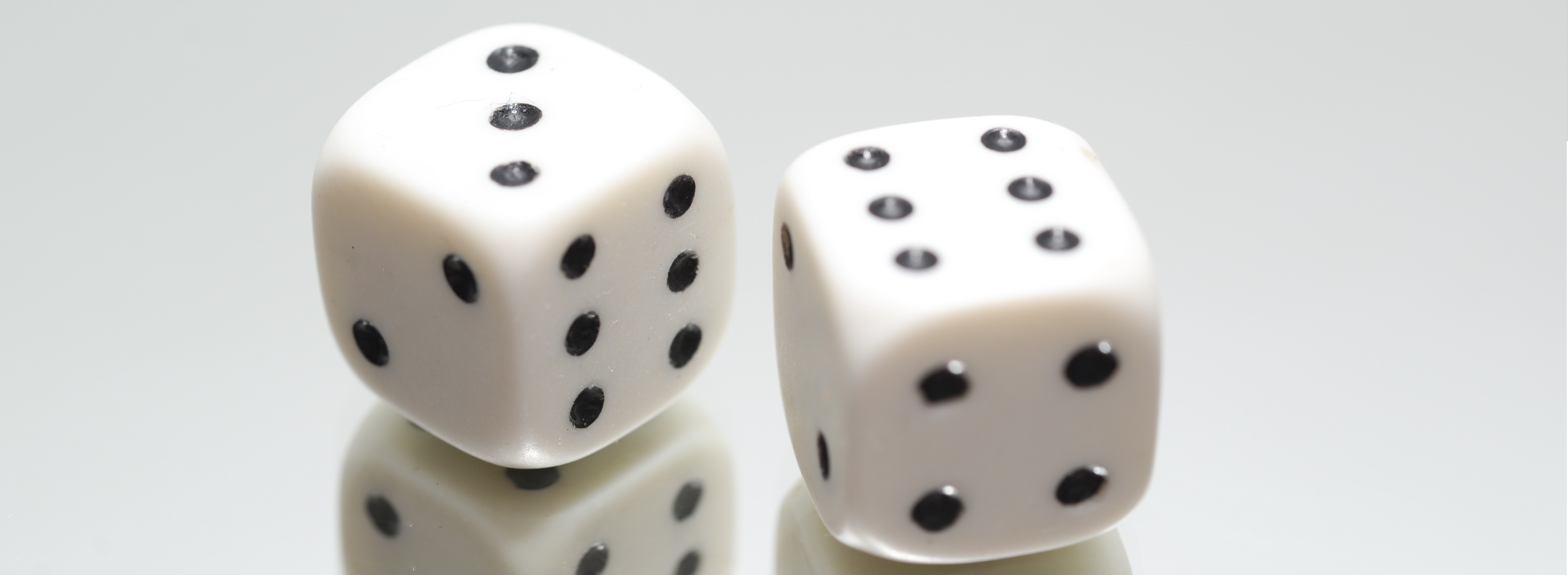
Efficiently filter risky solutions with our chance constraint.
Leveraging Constraint Scheduling: A Case Study to the Textile Industry
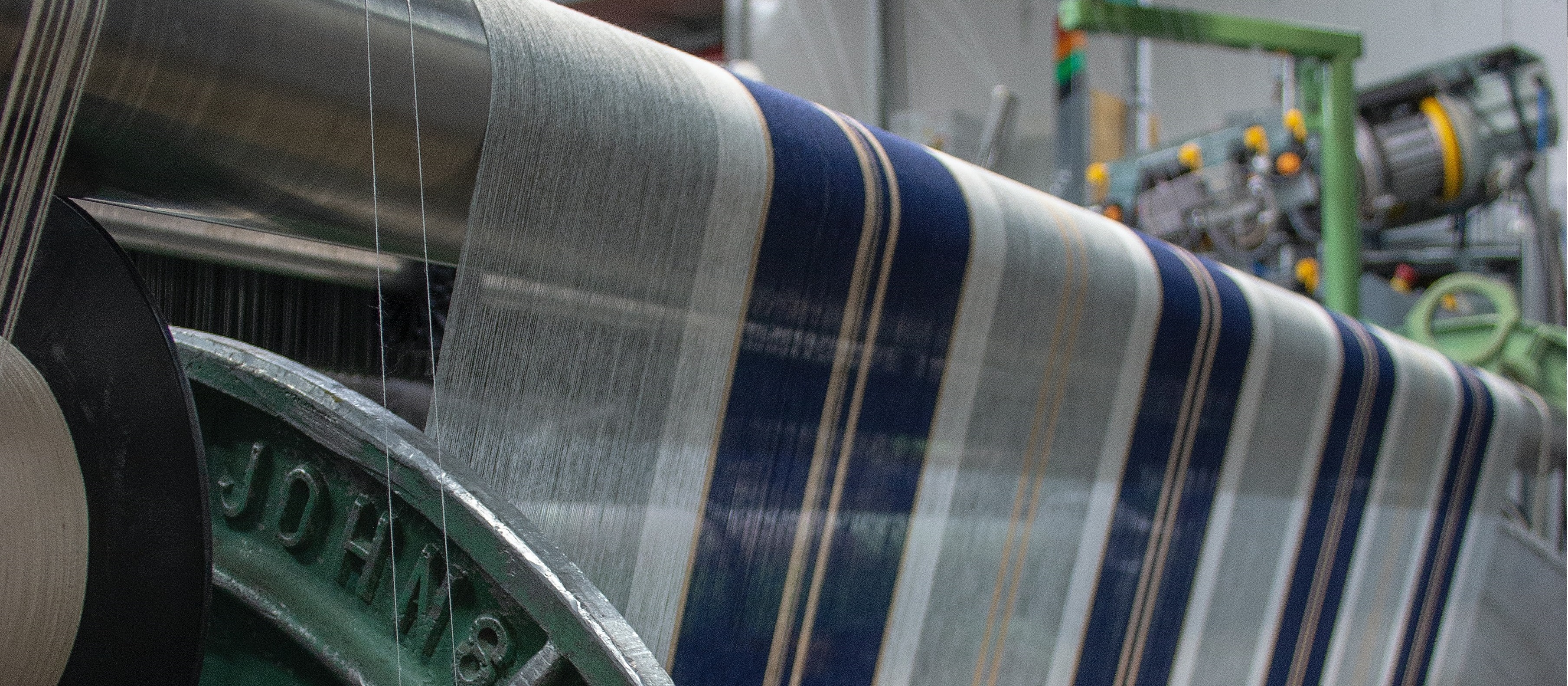
Warmstart your solve with a faster TSP solution.
2019
Multi-Resource Scheduling with Setup Times: An Application Case to the Textile Industry
Workshop on loom scheduling.